Most supply chain managers face hardships taking care of an adequate spare parts management system as they are always skeptical that stocking up on spares may not be in sync with efficiently managing operational costs. Therefore, as a supply chain manager, you are expected to produce multiple ways to perform efficient spare parts management.
As a supply chain manager, you are required to understand and evaluate the necessary spare parts that you require to run your system efficiently. It would be best if you had an in-hand plan that gives you a clear-cut approach towards the best industry practices. Spare parts management system is an element of a planned service management outlay that companies use to control the risk of equipment downtime. In this blog, you'll learn how to minimize that risk and use it to your benefit. Let's get into it!
Table of contents
- What is spare management, exactly?
- Why should you take advantage of a spares management plan in 2022?
- Things to keep in mind before creating an adequate spare parts inventory management system
- Analyzing strategy
- Regulating the work order process
- Functional spare parts inventory control
- Detailed understanding of lead times for multiple spare parts
- Stock-in new parts for new equipment
- Measuring total risk for types of equipment
- Taking appropriate security measure
What is spare management, exactly?
The main agenda of Spare Parts Management is to supply the right parts, in the adequate quantity, to the right spot, at the correct cost to quality ratio.
Effective management and maintenance of spare parts is an essential factor to the performance and cost of maintenance of pieces of equipment.
The overall outlook of Spare Parts Management encapsulates all functionalities from the supplier to the point of use, right from identification and coding, classification, acquisition, quality assessment, stocking policies, links to work planning, supplier management, and internal performance.
Why should you take advantage of a spares management plan in 2022?
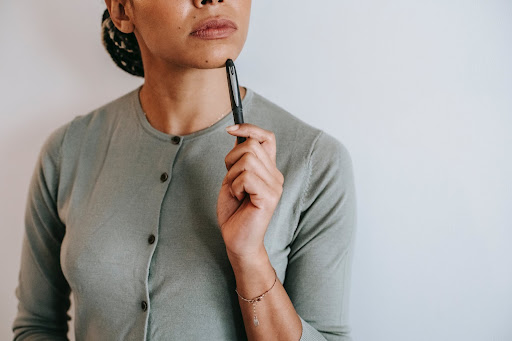
Spares management systems help you integrate your hardware with a software support tool that enables you to share your data regarding your operations and requirements. By integration of the hardware and software, you will be able to curate a list of spare parts that you will require, and you will be able to understand where you're lacking and what needs attention.
Here are certain benefits of spare parts management and how they can help you with your functionalities:
- It gives you the space to maintain low levels of excess inventory. Help you to reduce carrying and storage costs by gaining access to spare parts as and when required.
- Spares management allows you to be consistent with your service. The more consistent you are, the longer your operations will be in service and the better you'll be able to provide and meet the demands of your customers with your excellent services and support.
- Spares management improves your visibility, so your supply chain can determine where the need for a specific spare part is and where the spare parts are headed.
- With spares management, the equipment uptime has a visible enhancement as you cut down on the long period of equipment downtime and don't have the need to create revenue or find a new source to mend apart when it faces issues.
- Spare management assists with faster repairs and replacements for faulty parts and provides assistance for large-scale faults
Sure, having an in-house monitoring system can help you bypass many of these issues and help you to reap these benefits, but remember that it also has its fair share of limitations as you will withhold your limited knowledge about the equipment.
Whereas consulting with a third-party entity can provide you with the necessary data and information about the parts you deal with and can even suggest the industry's current trends. Take, for example, a third-party entity that can give you specific details about the life of the particular spare part and how long it can last while working efficiently.
This will help you to accumulate a specific part before the expiration period. Third-party partners also possess a more comprehensive range of inventory as they cater to a wide array of customers. This gives you the benefit of an extensive warehouse with the best possible parts in the market at reasonable costs. Thus, with the help of a third-party spares entity, you can efficiently optimize and manage your business.
Things to keep in mind before creating an adequate spare parts inventory management system
There are a few aspects to keep in mind before creating an adequate spare parts inventory management system. These factors can determine your carrying costs, performance interruption, and the efficiency of your operation. Here are some of the critical factors that have been analyzed and should be taken into consideration before creating an adequate spare parts inventory management system. Then, let's examine each in more depth.
1. Analyzing strategy
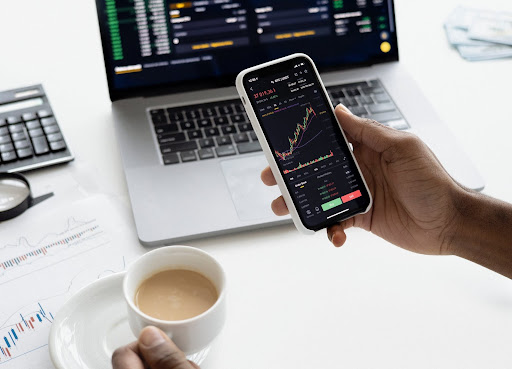
Analyzing your strategy for your operations is one of the first and foremost things to consider before creating effective inventory management involving spare parts. Here are certain aspects to take a look at
- You are analyzing and classifying data related to your business to enhance your business strategy.
- Make sure you look out for repeated failure patterns that can expose specific hidden issues hindering your growth.
- Using predictive management can help you use your resources efficiently and cut down on costs related to solving problems.
2. Regulating the work order process
Implementing an immediate and robust work order process goes a long way in efficiently managing your inventory. When you set and fix one standard work order process, ensure that the process is easy for everyone to follow and work with and make sure that you standardize it for everybody.
A high functioning work order must constitute proper guidelines covering all aspects – so that the inventory control system retains efficiency.
3. Functional spare parts inventory control
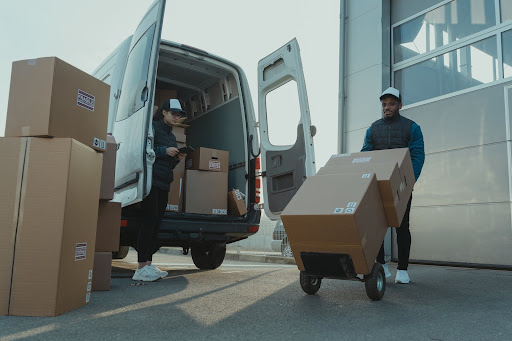
Using a computerized maintenance management system with designated inventory management software is another way to manage and control your inventory levels and helps you phase out repeated inventory monitoring.
4. Detailed understanding of lead times for multiple spare parts
A clear-cut understanding of all of your spare part lead times is necessary for developing an efficient spare part inventory management system. Lead time for a spare part is ultimate when considering the factors to stock and the volume in which it is done.
Here are certain aspects to keep in mind when trying to understand lead times for spare parts inventory:
- Creating made-to-order spare parts with longer lead times and expelling spare parts with shorter lead times. Always hold in pieces that have extended lead times.
- Make sure to have a few off-brand names in mind that are instantly available when you come across specific issues.
5. Stock-in new parts for new equipment
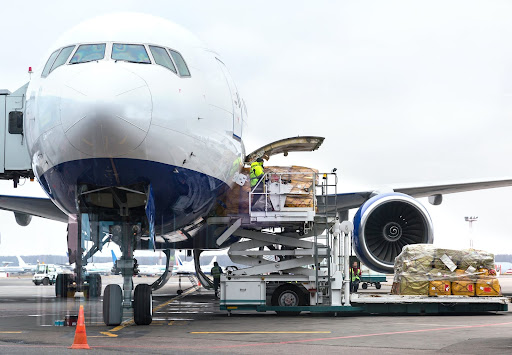
Here are a few things to keep in mind before stocking spare parts for brand-new equipment:
- Integrating with the operations strategy division to ensure planned budget and funds for spare parts of your equipment.
- Contact vendors to provide a list of endorsed essential components for the pieces of equipment you bought from them.
- Make use of present data to help with your decision-making on the necessary spare parts to stock on.
6. Measuring total risk for types of equipment
Calculating the risk for the pieces of equipment you have purchased is essential as you always have to be aware of the availability of the spare part and have to prepare yourself to stay equipped. Here are a few things to keep in mind during the calculation of risk for every piece of equipment you own:
- Predict an average of one-hour downtime for your firm in case of unavailability of spares.
- Work with present information and lead times for the spare parts of your equipment.
- Determine the cost and possible reasons for your gear to cease.
- Make a comparison table that denotes the cost of buying new vs. old spare parts as an alternative.
7. Taking appropriate security measures
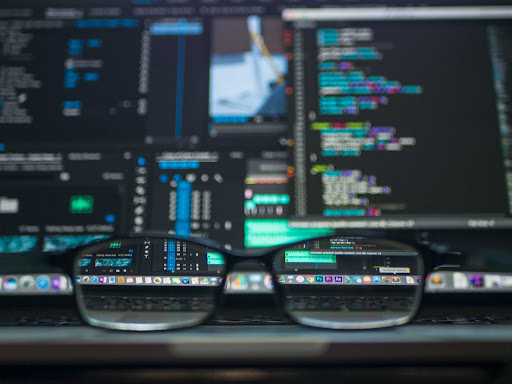
Giving access to your spare parts inventory warehouse is also critical for creating a secure spare parts management system. Make sure that there is limited access and that only the essential people get access to the spare parts inventory warehouse. This will eliminate inventory inaccuracies and protect your inventory.
Conclusion
Spare part inventory management is an aspect that gets overlooked for the most part. Its importance is only brought to light when the inventory costs need to be slashed down or when certain spare parts that are of necessity are costing you heavy downtimes.
At the end of the day, You need to understand the importance and value of an accurate inventory system with efficient spare parts management. With this knowledge, you can be sure that the parts you need are available when you need them and that your spare parts inventory is as efficient as possible. Know that this is a core aspect of the day-to-day operations of your company. Good luck!