Inventory management is a method of keeping track of inventory flow. It begins with the purchase of commodities and their storage, and continues with the outflow of raw materials or stock to the industrial units or the market, as appropriate. The process can be done manually or with the help of an automated system.
When the goods arrive on the premises, inventory management guarantees that these items, such as stock, raw materials, components, tools, and so on, are efficiently received, counted, sorted, arranged, stored, and maintained.
Supply Chain Management is incomplete without an effective inventory management system (SCM). It is responsible for monitoring the purchasing of production components from suppliers as well as the fulfilment of customer orders. This method is used by businesses to meet customer needs and increase sales. It also aids businesses in tracking product movement from manufacturing units to warehouses and finally to places of sale.
Table of Contents
- Importance of Inventory Management Techniques
- What are the 12 Popular Inventory Management Techniques?
- Minimum Order Quantity
- Just in Time Inventory Management
- FIFO and LIFO
- Reorder Point Formula
- ABC Analysis
- Lean Manufacturing System
- Batch Tracking
- 6 Sigma
- Lean Six Sigma
- Consignment Inventory
- Perpetual Inventory Management
- Demand Forecasting
Importance of Inventory Management Techniques
Inventory management is critical for eCommerce and online retail businesses. Inventory management aids in better planning and ordering of stock products by achieving a balance between demand and supply, which is vitally important for enterprises.
- Accurate inventory control, brands can fulfill orders on time.
- eCommerce and retail businesses can manage their cash flow opportunities with inventory control and planning.
- Small businesses can cut inventory labour expenses by using better inventory planning and management approaches.
- Businesses can acquire insight into hot-selling products by using an inventory management tool.
Companies can profit from inventory management by implementing a strategic plan that streamlines the process of controlling and maintaining inventory, as well as providing real-time data on inventory conditions and levels.
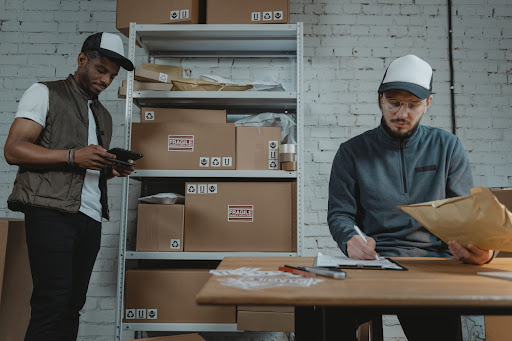
What are the 12 Popular Inventory Management Techniques?
Let's take a look at 12 of today's most popular inventory methods. These are some of the most successful ways for improving inventory control in your company.
1. Minimum Order Quantity
The smallest amount of stock that a supplier is willing to sell is known as the minimum order quantity (MOQ). You won't be able to acquire a product from that provider if you can't meet the MOQ.
Minimum order quantities are used by suppliers to improve earnings while simultaneously eliminating excess inventory and "bargain seekers."
The minimum order quantity is calculated based on your total inventory cost, as well as any extra costs you must pay before making a profit. MOQs, in other words, assist wholesalers in being profitable and maintaining a consistent cash flow.
2. Just in Time Inventory Management
Just-in-time Inventory management is the process of producing what is required at the time and in the quantity required. Many businesses use a "just-in-case" inventory management strategy, which involves keeping a modest amount of inventory on hand in case demand spikes unexpectedly.
Just in time inventory (JIT) management strives to achieve a zero inventory system. It works on a pull mechanism, which means that when an order comes in, it triggers a cascade response throughout the supply chain. This informs the employees that inventory must be ordered or production must commence on the required items.
Just-in-time inventory management has several advantages, including:
- Inventory that is less outmoded, outdated, or spoilt
- Minimizing or eliminating waste reduces waste and increases efficiency.
- Inventory turnover is maximised via storage and hoarding.
- By lowering your inventory, you can save money on insurance and rent.
- Because production takes place on a smaller, more focused scale, identifying and correcting production problems is faster.
- Keeping a healthy cash flow by only ordering stock when it's absolutely necessary
You can get a complete understanding of JIT here: Just-in-Time Inventory: Ultimate Guide
3. FIFO and LIFO
FIFO and LIFO are inventory valuation and profitability reporting accounting procedures.
First in, first out is what FIFO stands for. It is an inventory accounting system that states that the first items in your inventory are the first to go, implying that you should always get rid of your oldest stock first.
Last in, first out is abbreviated as LIFO. It is an inventory accounting system that states that the last goods in your inventory are the first to leave, implying that the newest stock is sold first.
You almost always have to utilise the FIFO rule if you're running a food business or otherwise dealing with perishable commodities. You'll wind up with obsolete inventory that you'll have to write off as a loss if you don't.
If you obtain a new batch of non-perishable homogeneous goods like brick or stone, you don't have to rearrange your warehouse or rotate batches because they'll be the first out anyhow.
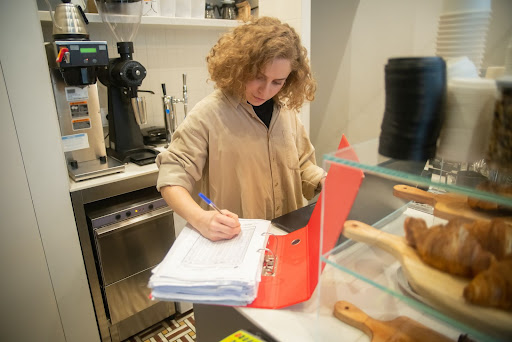
4. Reorder Point Formula
The reorder point algorithm tells you when it's time to replenish your inventory. When you reach the lowest amount of inventory you can sustain before needing more, you'll be notified.
The reorder point is calculated using the following formula: (Average Daily Unit Sales x Average Lead Time in Days) + Safety Stock.
You may quit being a victim of market ups and downs by using this method to consistently order the proper amount of stock every month.
5. ABC Analysis
ABC inventory analysis divides your inventory into three groups based on how much it costs to store and how well it sells.
A-Items: The most popular items that don't take up a lot of room in your warehouse or cost a lot of money.
B-Items: Items in the middle of the price range that sell frequently but cost more to store than A-Items.
C-Items: The rest of your inventory, which accounts for the majority of your inventory expenditures yet has the smallest impact on your bottom line.
Because it indicates which things you should replenish more frequently and which items you don't need to stock as frequently, ABC analysis helps you keep your working capital costs low. ABC analysis improves inventory turnover and cuts down on obsolete stock.
6. Lean Manufacturing System
The lean manufacturing system is also known as lean production or lean manufacturing. This approach is notable for maximising consumer product value and reducing waste without sacrificing efficiency.
The Toyota production method inspired this inventory tracking system, which aimed to prevent:
Muda: Everything in your production process that produces waste or limits your potential to make a useful product is referred to as muda.
Mura: Everything that causes efficient and inconsistent workflows is referred to as mura.
Muri: All loads or jobs that impose too much stress on your machines or personnel are referred to as this.
The following principles apply to all lean manufacturing systems:
- Lean manufacturing ensures that the consumer receives the most valuable product possible.
It lays out the actions and processes involved in producing valuable goods. - It goes through a procedure to ensure that all of your value-adding steps go off without stumbling blocks, delays, or disruptions.
- Materials are not stockpiled, and customers can receive their purchases in weeks rather than months since products are created just-in-time.
- The company's culture promotes lean thinking and process improvement.
This inventory management strategy helps you to manufacture the finest quality products while also increasing productivity and revenue by minimising or eliminating Muda, Mura, and Muri while following the five principles.
7. Batch Tracking
Lot tracking is a term used to describe how bats track. It's a method for efficiently tracing goods with batch numbers across the distribution chain.
Batch tracking allows you to know where your products came from, where they went, how much was transported, and, if they have an expiration date, when they expire, regardless of whether they are raw materials or finished goods.
The following are some of the advantages of using this inventory management method:
- Better relationships with suppliers
- Easy and fast recall
- Expiration tracking made easier
- Manual tracking causes fewer accounting errors.
8. 6 Sigma
This data-driven strategy, also known as Six Sigma, intends to minimize product defects to 99.99966 percent defect-free products over time, or 3.4 defective parts per million.
Six Sigma practitioners use statistical models to develop and enhance a company's production process until it reaches the Six Sigma level.
DMAIC, which stands for define, measure, analyse, improve, and control, is a five-step procedure that is commonly used.
The DMAIC process creates a cycle of continuous improvement in manufacturing procedures by combining data and quantifiable targets. DMAIC is effective for improving existing processes, whereas DMADV is used by Six Sigma to create new processes, products, or services.
Define, measure, analyse, design, and verify are the acronyms for define, measure, analyse, design, and verify.
It serves as data and in-depth analysis to assist you in developing efficient procedures or a high-quality product or service.
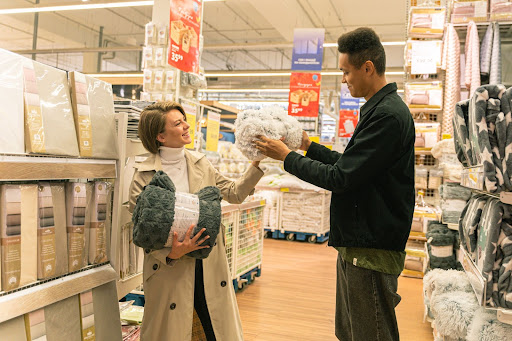
9. Lean Six Sigma
Lean Six Sigma combines with Six Sigma with lean manufacturing to build a comprehensive system that eliminates waste and minimises process variation in order to streamline production and improve product output.
Six Sigma processes are the backbone of Lean Six Sigma, which is intended to deliver focused improvements in production. Many tools and approaches from the lean approach are also used to decrease inefficient procedures and steps.
10. Consignment Inventory
A seller or wholesaler, known as a cosigner, agrees to give their goods to a cosine e, most typically a retailer, without the store paying for the items up front. The products remain the cosigner's property, and the cosigner is only charged when the things are sold.
As long as both parties are ready to share the risks and profits, this is a win-win situation.
Low inventory carrying costs, direct distribution to retailers, and new markets are all benefits for vendors. Retailers benefit from decreased costs of ownership, less risk, and enhanced cash flow.
11. Perpetual Inventory Management
Perpetual Inventory Management is frequently referred to as a continuous inventory system. Permanent inventory systems keep track of sold and stocked inventory in real time, automatically updating your accounting system whenever a sale is made, new inventory is received, or inventory is used.
This data is delivered to a central hub, where authorised staff can view it at any time. This system's benefits include the capacity to handle several sites swiftly, more accurate forecasting, and proactive inventory turnover tracking.
12. Demand Forecasting
The technique of projecting what your consumers will buy, when they will buy it, and how much of it they will buy is known as demand forecasting.
You can use a variety of informal ways, such as guessing, or quantitative methods, such as analysing previous sales data.
Whether you're using demand forecasting to plan production, enter a new market, or manage inventory, it'll help you make smarter decisions for managing and expanding your firm.
The following are some of the best demand forecasting practises:
- Creating a monthly process that can be repeated
- Choosing what to measure and how frequently to measure
- Bringing data from all of your sales channels together
- Updating and maintaining real-time data
Determine the appropriate inventory management system for your firm based on company data and goals. Then, to get the most out of it, make sure you have the tools you'll need to make it as simple as possible.
Conclusion
Inventory Management is an important aspect of every firm. With a good inventory management system in place, the company may save money on warehousing, inventory carrying, ordering, and obsolescence charges, among other things. It improves the company's supply chain. Managers can predict the amount of production at which they will need to place fresh inventory orders. As a result, businesses should take all necessary precautions to ensure that their inventory management and control systems are up to date.